Most of the polyurethane used in cushions, fibers, thermal insulation materials, paints and the like are produced using highly-toxic isocyanate compounds as a raw material. The research group of Associate Professor TSUDA Akihiko of Graduate School of Science, Kobe University in cooperation with AGC Inc. succeeded in using a jointly developed fluorinated carbonate as the raw material in the development of a novel polyurethane synthesis method, which does not use isocyanate. They enabled the synthesis of polyurethane by:
(1) Synthesizing fluorinated carbonate using the photo-on-demand synthesis method developed by Kobe University;
(2) Reacting this with a general purpose or specific alcohol (diol) to synthesize a polyurethane precursor (biscarbonate); and
(3) Finally, enabling the synthesis of polyurethane by reacting this with a commercially available amine (diamine).
This new method can be used in a broad range of polyurethanes, from widely available products to specialized produce, in addition to prepolymers. This facilitated the manufacture of high-quality polyurethane featuring almost no discoloration, without impurities such as acids and the like and with a regular polymer structure, and enabling molecular weight control.
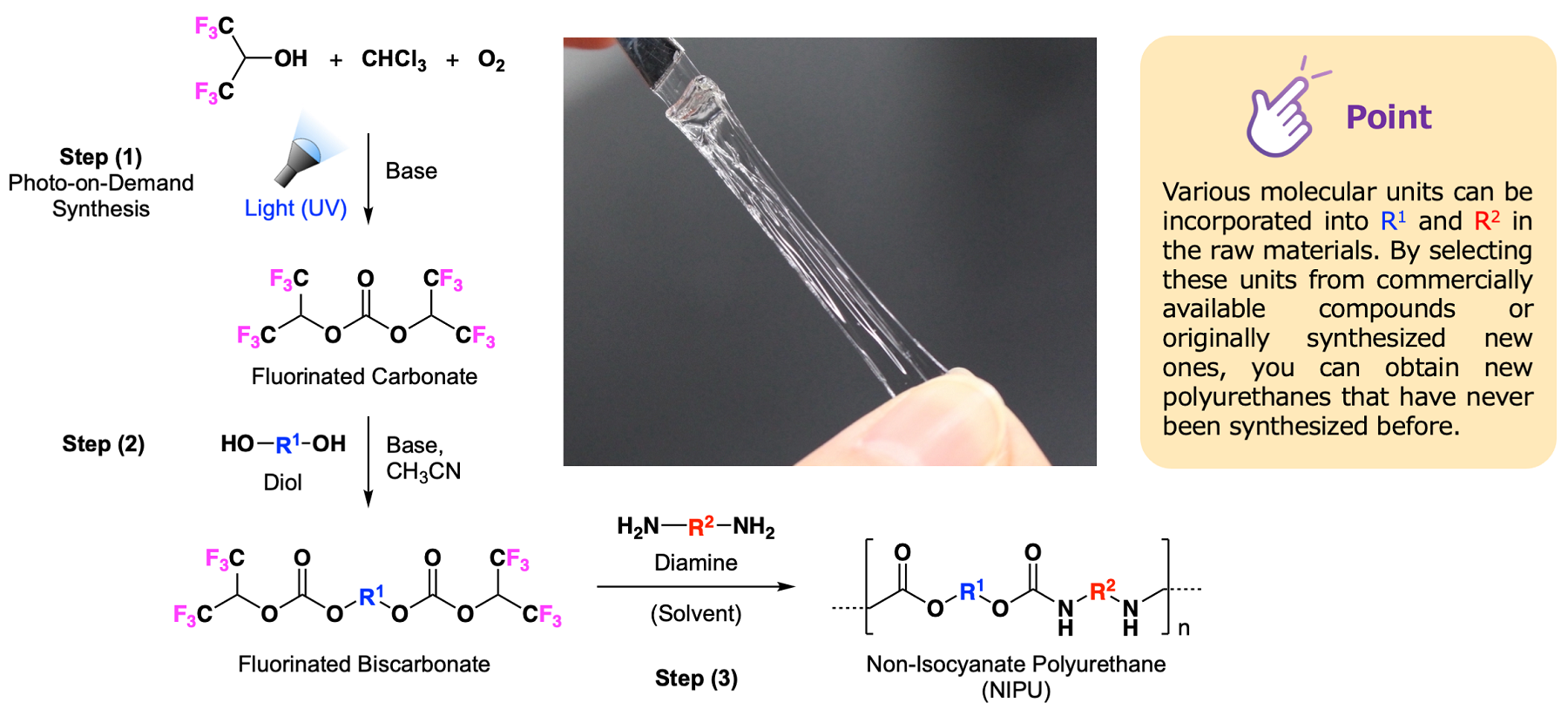
A Novel Synthetic Method of Non-Isocyanate Polyurethane (NIPU), Credit: TSUDA Akihiko, Restriction:None
This research resulted in the filing of a Japanese patent application in May 2020 which was filed internationally in May 2021, and after publication of the patent application, was published on the website of the Japanese Chemical Society, Bull. Chem. Soc. Jpn. on July?21 2023.
Main points
- A manufacture method of polyurethane not using isocyanate (a highly toxic raw material).
- Achieves an environmentally friendly polyurethane manufacture method not using either solvents or catalysts.
- By using a fluorinated carbonate jointly developed by Kobe University and AGC, enables the synthesis of a variety of polyurethanes from the conventional raw material of polyurethane in a safe, inexpensive, simple and environmentally friendly manner.
- This synthesis method exhibits utility and versatility and enables the synthesis of 12 types of general-purpose urethanes and one (special) type of fluorinated polyurethane.
- Because the polymerization reaction proceeds at a lower temperature than the non-isocyanate methods reported to date, a high-quality polyurethane is obtained which is highly transparent without discoloration and has high strength and high elasticity (a high molecular weight having a regular structure).
- The fluorinated alcohol which is the only byproduct can be recovered and can be reconverted to fluorinated carbonate in the photo-on-demand organic synthesis method.
- This is a novel and very useful synthesis method enabling the replacement of several of the current isocyanate methods and contributes to implementing a sustainable society.
- This is an example of the success of university-industry cooperation between Kobe University and AGC, which was in receipt of support from the JST A-STEP* cultivating success (2018 – 2021) program (*Adaptable and Seamless Technology Transfer Program through target-driven R&D)
Background of the research
Polyurethane is highly elastic, wear resistant and durable, and is used, for example, in cushions, fibers, thermal insulation materials, dyes, adhesives and automobile parts. Polyurethane is an industrially-important polymer material, with an estimated worldwide market value of 75 billion dollars (2023 Grand View Research Inc. investigation). Most polyurethane is currently synthesized by means of reacting diisocyanate with diol (FIG. 1, reaction (a)). However, isocyanate compounds are highly toxic, and the tightening of regulations on the use of diisocyanate are progressing recently, particularly in the EU, because of health and environmental concerns. In recent years, active research is proceeding into the synthesis of polyurethane without using isocyanate compounds with a view to implementing a sustainable society. However, most of current methods have low utility, high environmental costs, and the quality of the derived polyurethane is low as well as being expensive, and are not practicable because of the variety of problems associated with them.

Credit: TSUDA Akihiko, Restriction:None
In this background, Kobe University Associate Professor Tsuda and AGC, with the support of funding from the JST A-STEP program, combined their efforts to jointly develop a novel polyurethane synthesis method (FIG. 1, reaction (b)). University-industry cooperation between the research group of Associate Professor Tsuda, pioneers of the Photo-on-demand organic synthesis method and AGC, a manufacturer of fluorinated compounds and polyurethane raw materials, created a new academic field and industrial activity based on the development of a new polyurethane synthesis method and functional materials.
Content of the research
A variety of fluorinated biscarbonates (BFBC) were synthesized (FIG. 2) by a condensation reaction of fluorinated carbonates, synthesized in the photo-on-demand synthesis method from fluorinated alcohols and chloroform, with diols. The BFBC generated could be purified by merely drying the derived sample solution at reduced pressure, enabling the quantitative derivation of the target substance by a simple operation.

Credit: TSUDA Akihiko, Restriction:None
The synthesis of a non-isocyanate polyurethane (NIPU) with an average molecular weight in excess of 10,000 was achieved by polycondensation of the derived BFBC with diamine. The NIPU synthesized without solvent was only slightly discolored at over 120°C, and that discoloration was not observed up to 100°C. On the other hand, if a solvent is used, it can be polymerized at a lower temperature, and a high molecular weight colorless NIPU is derived at a high-yield. They were able to form a highly-elastic colorless and transparent polyurethane by an appropriate combination of BFBC and diamines in hard and soft segments (FIG. 3, Reactions (1) and (2)). They also succeeded in synthesizing a novel fluorinated polyurethane which is a colorless transparent oil (FIG. 3, Reaction (3)).
The variety and types of polyurethane synthesized, with a range from general purpose to specific applications, have the following benefits when compared to the previously reported synthesis methods of NIPU:
(1)?Any NIPU can be synthesized which employs commercially available diols or diamines employed in the industrial manufacture of polyurethane by the isocyanate method, or which was originally used in the synthesis of NIPU.
(2)?This is a synthesis method which does not use organic bases, metallic catalysts or solvents in the synthesis, such that a high quality NIPU can be derived which does not contain any of them.
(3)?The average molecular weight and terminal functional groups can be controlled by the admixture ratio of BFBC and the diamines. An NIPU prepared by this method with the molecular weight of the order of 10,000 can be employed as a prepolymer in order to synthesize even larger polymers or networked polymers.
(4)?The reagents, solvents and eliminated fluoroalkyl alcohols can basically be recovered, and be re-utilized in the synthesis of these NIPU.

Credit: TSUDA Akihiko, Restriction:None
Future perspectives
The conventional polyurethane synthesis method using isocyanate has advantages from a cost perspective. However, the novel and useful non-isocyanate polyurethane (NIPU) synthesis method using these newly developed fluorinated carbonates and fluorinated biscarbonates can replace several conventional methods with a view to implementing a sustainable society, in addition to enabling the creation of functional polyurethanes which conventional methods cannot synthesize. Research is proceeding at present, both from an academic and industrial perspective, with a view to bringing this process to market.
Acknowledgements
This research was in receipt of funding support from the Japan Science and Technology Agency (JST) Adaptable and Seamless Technology Transfer Program through Target-driven R&D (A-STEP), University-industry Cooperative phase results promotion research topic: "The development of high-functionality/high-added-value polyurethane materials by means of a safe manufacture process involving the inclusion of fluorinated carbonates as a key intermediate" (Project name: AGC Inc., Project representative:Takashi Okazoe, Research Representative: Akihiko Tsuda)
Patent Information
- Title of the patent
- Manufacture method of polyurethane
- Japanese Patent Application
- JP2020-83148, Patent Application date: May 11, 2020
- International Patent Application
- PCT/JP2021/17511, Patent Application date: May 7, 2021
- Laid-open publication
- WO 2021/230151 A1 [Nov. 18, 2021]
- Inventors
- TSUDA Akihiko, OKAZOE Takashi, WADA Hiroshi, TANAKA Hideaki, SUNAYAMA Yoshitaka, KAKIUCHI Toshifumi
- Patent Applicants
- Kobe University and AGC Inc.
Journal Information
- Title
- “Non-Isocyanate Polyurethane Synthesis by Polycondensation of Alkylene and Arylene Bis(fluoroalkyl) Bis(carbonate)s with Diamines"
- DOI
- 10.1246/bcsj.20230066
- Authors
- : Sasuga Hosokawa,1,§ Akihiro Nagao,1,§ Yuka Hashimoto,1,§ Ayako Matsune,1 Takashi Okazoe*,2 Chitoshi Suzuki,2 Hiroshi Wada,2 Toshifumi Kakiuchi,2 Akihiko Tsuda*,1
* Corresponding author, § Equal contribution
1. Kobe University, Graduate School of Science
2. AGC Inc. - Journal
- Bulletin of the Chemical Society of Japan